Detecting potential differences
Communication disturbances attributable to potential differences in CAN units have often been underestimated. They usually go unnoticed. Such errors can nonetheless be detected, measured, and rectified.
Serial bus systems are a decisive factor for determining performance capabilities of complex manufacturing systems in many industries. The whole electronic communication is realized within complex systems, meaning that the highest demands must be placed on the reliable functioning of serial bus systems. Measuring devices for bus analysis – both at the time of installation and for permanent status monitoring and early error detection – are in the meantime indispensable. On the other hand, such devices have to date remained oblivious to disturbances in data communication. These disturbances result from inadequate potential equalizations.
Until a few years ago, it was assumed that such problems were caused by system-internal reasons. Today, however, we know that external influences such as electromagnetic interference or inadequate potential equalization are increasingly the culprits where communication is disturbed. Outdated or inappropriate framework conditions (e.g. grounding and potential equalization) also open the door wider to previously ignored sources of disturbance. High-frequency currents, for example, often use the shielding of a data line as their return path, even when a potential equalization conductor is provided precisely for this purpose. That results in correspondingly error-prone communication or even loss of the whole system functionality. Gemac has applied this knowledge in its developments: the latest CANtouch diagnosis device now also detects such error sources – in addition to the established measurements of physical bus characteristics.
Bus diagnosis
CAN uses a differential signal to compensate for the influences of external interferences. In other words, the data signal is transmitted in two lines, which are inverted to each other (CAN_H and CAN_L). The difference between these two lines generates the signal received by each CAN transceiver. Disturbances on the bus can prevent correct detection of the bit stream. Gemac’s diagnosis systems permit evaluation of the differential signal in the form of a general quality value, of the disturbance-free voltage range, and of the edge steepness. CANtouch provides an absolute measurement of the individual signals CAN_H and CAN_L against a reference potential. This lets it detect an error source which is frequently encountered in system installations: the so-called “common-mode voltage”. In a differentially operating transfer system, such as CAN, the term “common-mode voltage” is used for the voltage of both signals relative to a common reference potential. This is normally CAN_GND, which in each device is connected to CAN_V-. On a CAN network, both signal lines (CAN_H and CAN_L) should display a common-mode voltage of 2,5 V in the recessive state. For a number of reasons, the common-mode voltage of the devices may manifest an offset. CANtouch is able to determine this voltage offset directly. It could also be detected indirectly via measurement of the shield voltage. In practice, two forms of wiring can lead to potential differences between devices. In the first variant, all bus nodes receive their power supply via the CAN cable; in the second, each device possesses its own power supply.
Potential confusion
Let us first consider the case where all connected devices are supplied via the four-wire CAN cable (Figure 1).
Two of the four wires in the cable are used for the CAN communication and the remaining two for the supply voltage. When the wiring is installed, the shield initially has no low-resistance connection to a particular potential, as the connection to V- in each device is usually realized by way of a parallel resistor (1MOhm) and capacitor (10nF). For a low-resistance connection, the shield should be connected with V- and the protective ground at the central voltage supply. This has the following effect: Due to the line resistance, the current load of the individual CAN devices results in a voltage drop (Delta‑U) on the supply lines.
This raises the voltage level of CAN_V- at each CAN device and leads to a negative voltage offset of the shield voltage measured against CAN_V-. This “normal” shield voltage should lie in the range from approximately 0 V to ‑4 V. CANtouch reports greater shield voltages or a shield which is not connected to CAN_V- as errors. The voltage drop in the cable will at the same time result in different GND potentials for the CAN transceivers. This is manifested as a shift in the levels of the signal voltages, which each CAN transceiver “sees” for itself. The CAN system only permits shifts within the range of ‑2 V to +7 V. The CAN transceivers expect the signal voltages to lie within this range. Even though newer circuits tolerate a wider range of ‑7 V to +12 V, exceeding the expected range may lead to communication errors and, in an extreme case, eventually also to the destruction of the transceiver (Figure 2).
CANtouch thus determines the maximum voltage offset among all bus nodes – the so-called “worst-case total common-mode voltage” – and issues a warning if the limit values are exceeded (Figure 3). In addition, a graphical visualization shows whether the voltage offset lies above or below the present connection position. All absolute measurements are performed relative to V- on the 9‑pin D‑Sub connector (Pin 6). CANtouch even offers the possibility to switch the reference ground to an integrated 4 mm socket. This enables
the individual ground potentials of the CAN devices to be measured without needing to reconnect the test device, and thus potential differences to be detected faster. A simplified evaluation system using a combination of traffic lights and smileys assists the user.
Resisting temptation
It is important to resist the temptation to connect the shield to CAN_V- on all devices because the operating current of the devices would then flow back via the shield, as it has a lower resistance than CAN_V-. The coupling of interferences into the signal lines is then almost inevitable. As a remedy, the voltage supply can be realized to the middle of
the network, or else a supply with several power supplies can be provided. The use of CAN cables with a lower loop resistance for CAN_V+ and CAN_V- is another possibility. The CANtouch wiring test is able to measure the loop resistance of the cable.
The right cable
Standard limit values are reached relatively quickly in practice, as shown by the following example: To remain within the range of ‑2 V to +7 V as defined by ISO 11898 – 2, a
symmetrical potential difference of maximum 4,5 V above and below 2,5 V is permissible (2,5 V – 4,5 V = ‑2 V and 2,5 V + 4,5 V = +7 V). Taking a typical CAN cable with a cross-section of 0,22 mm², a line resistance of 185 Ohm/km, and an assumed total current load of 100 mA for all devices, the permissible potential difference is already reached at a
line length of approximately 240 m (and at a current of 1 A already after 24 m). An improvement can be achieved by choosing a CAN cable with a larger cross-section. At a cross-section of 0,34 mm², the loop resistance is reduced to 115 Ohm/km, at 0,50 mm² to 78 Ohm/km, and at 0,75 mmm2 to just 52 ohm/km.
A false shield is no solution
In conjunction with more extensive installations, it is not uncommon to find cabling configurations which provide an individual power supply to each bus node (Figure 4). In most cases, this is realized with a two-wire CAN cable.
Here, too, there is a risk of potential differences if the devices are not interconnected to provide potential equalization. In practice, the shield is frequently abused for the purposes of potential equalization. The equalizing current which flows through the shield, however, is itself already a possible source of disturbances for the CAN communication and should thus be eliminated as a possible solution from the very beginning. CANtouch is able to spot such wiring problems by way of the – now possible – measurements of the shield and common-mode voltages. The handheld diagnosis device is the industry-compatible equivalent to a smartphone. For the first time, system operators, technicians and developers are in a position to perform physical and logical bus analysis via an intuitive touchscreen. The device with a 4,3‑inch color display is ready for immediate mobile use without an additional PC. Similar to a smartphone, the user takes his diagnosis device directly to the CAN system, connects it with the cable and immediately receives reliable measurement results – without stopping the system. The individual measuring functions are operated interactively and dynamically by way of applications (“apps”) based on finger gesture control. A simplified evaluation procedure according to the traffic light principle and with the help of smileys supports the user in the fast evaluation of the measurement results.
CANtouch this…
The handheld CANtouch is the industrial-suited answer to smartphones. First-time facility operators, engineers and developers can analyze physical and logical values of a bus with an intuitive touchscreen. It is quick and mobile to use without an additional PC. So a user can simply connect directly to a CAN system with a cable and gets reliable values within minutes without stopping the system. This not only saves time, also it saves also a lot of money if you can get an early error warning. Fix problems before they stop your bus. The single measurements are used interactive and dynamic over apps and finger gestures. A simple rating system with ample colors and smileys supports the user to quickly rate the measured values. The 4,3‑inch color display makes it possible to show the measurements with appealing graphics.
Authors: Hendrik Stephani (Developer Fieldbus diagnosis), Antje Wappler (Marketing)
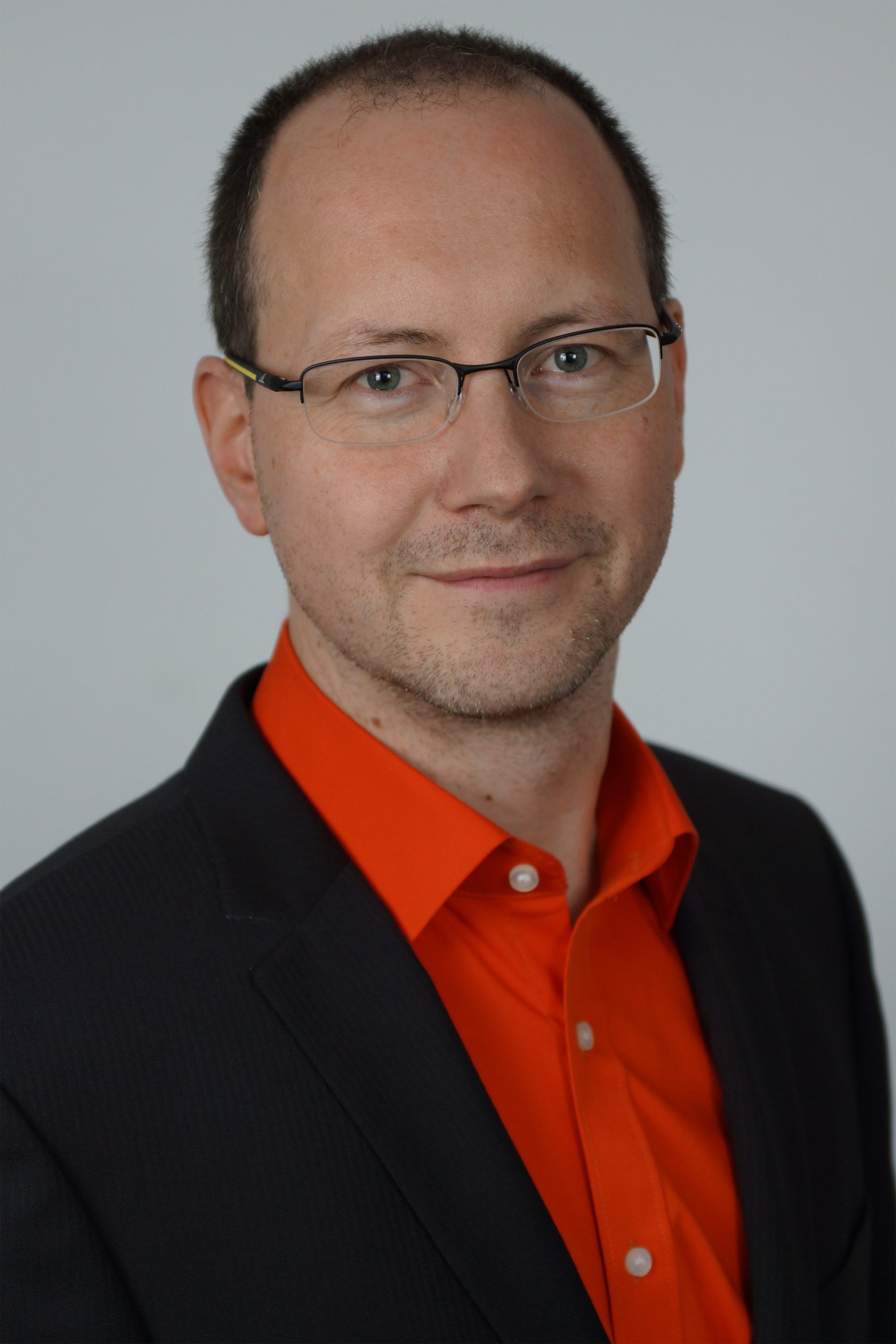
Hendrik Stephani
Hendrik Stephani has developed capable tools for fieldbus diagnosis for 20 years.